5. PRUEBAS HIDRÁULICAS (NEUMÁTICAS)
5.1. Requerimientos generales
5.1.1. Se realizan pruebas hidráulicas (neumáticas) para verificar la resistencia y densidad de equipos, tuberías, sus partes y unidades de montaje, cargadas con presión. 5.1.2. Las pruebas hidráulicas se realizan: 1) después de que el fabricante haya fabricado los equipos o elementos de tubería suministrados para la instalación; 2) después de la instalación de equipos y tuberías; 3 en durante la operación equipos y tuberías cargados con presión de agua, vapor o mezcla vapor-agua. 5.1.3. En lugar de pruebas hidráulicas, se permite realizar pruebas neumáticas de equipos y tuberías cargados con presión de gas, operando al vacío, en contacto con un refrigerante de metal líquido, así como carcasas de seguridad (carcasas) de centrales nucleares con reactores de neutrones rápidos y protectores. conchas ACT. La posibilidad de tal reemplazo debe ser aprobada por Gosatomnadzor de Rusia. Está permitido no realizar pruebas hidráulicas (después de la fabricación y durante la operación) de cascos experimentales y de investigación. reactores nucleares operando bajo la presión del peso del líquido que los llena, siempre que durante el proceso de fabricación se realice un control del 100% de las soldaduras por método de detección de fallas ultrasónicas o método radiográfico y métodos de detección de fallas superficiales. 5.1.4. Las pruebas hidráulicas (neumáticas) después de la instalación y durante la operación se llevan a cabo dentro de los límites de tiempo especificados en la cláusula 8.2.6. 5.1.5. Es obligatorio realizar pruebas hidráulicas (neumáticas) después de la instalación durante la puesta en marcha de equipos y tuberías, así como durante la operación (con la excepción de los casos de reparación estipulados específicamente en este documento). 5.1.6. Las pruebas hidráulicas de piezas o unidades de ensamblaje de tuberías fabricadas en los sitios de instalación pueden combinarse con pruebas hidráulicas una vez finalizada la instalación. 5.1.7. Los equipos y tuberías después de la fabricación e instalación deben someterse a pruebas hidráulicas antes de aplicar protección. revestimientos anticorrosión o aislamiento térmico. En equipos y tuberías que estén en contacto con un refrigerante de metal líquido durante la operación, se permite aplicar aislamiento térmico antes de las pruebas hidráulicas con el refrigerante especificado. Se permite realizar metalizaciones (sin aplicar revestimientos) uniones soldadas tuberías antes de la prueba hidráulica, si esto no se puede hacer después de que se complete la instalación, que debe especificarse en documentación de diseño . 5.1.8. Las pruebas hidráulicas (neumáticas) de equipos y tuberías durante la operación deben realizarse después de retirar el aislamiento térmico en los lugares especificados en la cláusula 2.1.9, así como en la documentación de diseño. 5.1.9. Las pruebas hidráulicas de piezas individuales y unidades de montaje de equipos y tuberías después de su fabricación no se pueden realizar en los siguientes casos: 1) el fabricante realiza pruebas hidráulicas de estas piezas y unidades de montaje como parte de unidades de montaje ampliadas o productos; 2) el fabricante de equipos que no contengan uniones soldadas I e I y categoría B de equipos fabricados con aceros de clase perlítica o aceros con alto contenido de cromo realice un control ultrasónico y radiográfico continuo del metal base y las uniones soldadas, y de los aceros austeníticos y aleaciones de hierro y níquel: control radiográfico continuo del metal base y las uniones soldadas, sujeto a todos los demás requisitos de la PC y la documentación de diseño; 3) el fabricante de equipos del grupo C fabricados con aceros de clase perlítica y aceros de alto contenido de cromo realiza ensayos ultrasónicos continuos de todas las uniones soldadas, así como sus ensayos radiográficos en un volumen doble con respecto al PC prescrito, y de aceros austeníticos y hierro - aceros al níquel - ensayo radiográfico continuo de todas las uniones soldadas; en este caso, se deben observar todos los demás requisitos de la PC y la documentación de diseño; 4) el fabricante de piezas y unidades de ensamblaje de tuberías de los grupos B y C hechas de aceros de clase perlita y aceros con alto contenido de cromo realiza pruebas ultrasónicas continuas de todas las uniones soldadas, así como pruebas radiográficas de las uniones soldadas II a, II para las categorías en la cantidad del 100%, categorías II c, II nv y III a - en la cantidad del 50%, III c - en la cantidad del 25%, y de aceros de la clase austenítica - control radiográfico continuo de todas las uniones soldadas, mientras que se deben observar todos los demás requisitos de la PC y la documentación de diseño; además, inspección adicional por capilaridad o partículas magnéticas de superficies maquinadas (cavidades, transiciones, codos de tubería, etc.) e inspección ultrasónica o radiográfica de metal en áreas de concentración de tensión y en áreas sujetas a deformación de más del 5% durante la fabricación (codos y extremos prolongados de tuberías, cuellos prolongados, etc.) y en la medida que lo establezca la documentación de diseño (para tuberías del grupo C, no se podrá realizar este control adicional). 5.1.10. Los estándares de evaluación de calidad para el control de acuerdo con la cláusula 5.1.9 deben adoptarse para el metal base de acuerdo con los estándares o especificaciones para los materiales relevantes y productos semiacabados, y para uniones soldadas, de acuerdo con el PC. 5.1.11. No se pueden realizar pruebas hidráulicas (neumáticas) de piezas individuales (por ejemplo, tuberías) en el fabricante si han pasado las pruebas hidráulicas en el proveedor de estos productos y después de eso no han sido sometidas a operaciones durante las cuales el material de estos piezas ha sufrido una deformación plástica. 5.1.12. Las pruebas hidráulicas (neumáticas) después de la fabricación de elementos de equipo y tuberías cargadas durante la operación con presión externa pueden llevarse a cabo bajo carga. presión interna.5.2. Determinación de la presión de pruebas hidráulicas (neumáticas)
5.2.1. La presión de prueba hidráulica debe determinarse al menos mediante la fórmula:(línea de fondo)
Y no más que la presión a la que se esfuerza la membrana total igual a 1,35 [ ] el, y la suma de los esfuerzos generales o locales de membrana y de flexión generales llegará a 1,7 [ ] el(limite superior). En la fórmula anterior Para = 1.25 para equipos y tuberías y Para= 1 para carcasas protectoras y carcasas de seguridad (carcasas), R - presión de diseño cuando se prueba en la planta del fabricante o presión operacional durante las pruebas después de la instalación y durante el funcionamiento, [ ] el- tensión admisible nominal a la temperatura de prueba hidráulica T h Para el elemento estructural, [ ] T - tensión nominal admisible a la temperatura de diseño T elemento estructural considerado. Para elementos cargados con presión externa, también se debe cumplir la siguiente condición:
R h 1,25 [R].
Nota. valores [ ] el , [ ] T, esfuerzos generales y locales de membrana y de flexión generales; [ R] - la presión externa admisible a la temperatura de prueba hidráulica se determina de acuerdo con las normas de cálculo de resistencia. 5.2.2. Bajo presión R hasta 0,49 MPa (5 kgf / cm 2) valor R h debe ser mas de 1.5 R, pero no menos de 0,2 MPa (2 kgf/cm 2). Bajo presión R más de 0,49 MPa (5 kgf / cm 2) valor PAG h debe determinarse a partir de las condiciones de la cláusula 5.2.1, pero no menos de ( R + 0,29) MPa (( R+ 3) kgf/cm 2). Estos requisitos no se aplican a equipos y tuberías con refrigerante de metal líquido. 5.2.3. En el caso de que se realicen pruebas hidráulicas (neumáticas) en un sistema o circuito compuesto por equipos y tuberías que operen a diferentes presiones de operación y (o) temperaturas de diseño, o que estén hechos de materiales con diferentes [ ] el y/o [ ] T, entonces la presión de las pruebas hidráulicas (neumáticas) de este sistema (circuito) debe tomarse igual a valor mínimo el límite superior de las presiones de prueba, seleccionado entre todos los valores relevantes para los equipos y tuberías que componen el sistema (bucle). 5.2.4. Los valores de presión de prueba hidráulica para equipos y unidades de ensamblaje (bloques) de tuberías deben ser indicados por el fabricante en el pasaporte del equipo y el certificado de fabricación de piezas y unidades de ensamblaje de la tubería. Los valores de presión de las pruebas hidráulicas (neumáticas) de los sistemas (circuitos) deben ser determinados por la organización de diseño e informados al propietario de la empresa del equipo y las tuberías, que especifica estos valores sobre la base de los datos contenidos en el pasaportes de los equipos y tuberías que completan el sistema (circuito).
5.3. Determinación de la temperatura de pruebas hidráulicas (neumáticas)
5.3.1. Las pruebas hidráulicas (neumáticas) de equipos y tuberías deben llevarse a cabo a una temperatura del medio de prueba en la que la temperatura del metal de los equipos y tuberías probados no sea inferior a la temperatura mínima permitida, determinada de acuerdo con el cálculo de resistencia. Normas. En este caso, en todos los casos, la temperatura de ensayo y medioambiente no debe ser inferior a 5 °C. 5.3.2. Se permite realizar pruebas hidráulicas (neumáticas) después de la fabricación o instalación sin realizar el cálculo de acuerdo con la cláusula 5.3.1 a una temperatura del metal de al menos 5 °C en los siguientes casos: 1) el producto está hecho de corrosión- aceros austeníticos resistentes, no ferrosos o de aleación de hierro-níquel; 2) el producto está hecho de materiales con un límite elástico a una temperatura de 20 ° C inferior a 295 MPa (30 kgf / mm 2) y tiene el espesor de pared más grande de no más de 25 mm; 3) el producto está hecho de materiales con un límite elástico a una temperatura de 20 ° C inferior a 590 MPa (60 kgf / mm 2) y. tiene el mayor espesor de pared no más de 16 mm. También se permite, sin realizar el cálculo según la cláusula 5.3.1, determinar la temperatura mínima permisible del metal durante las pruebas hidráulicas. T h de las siguientes proporciones: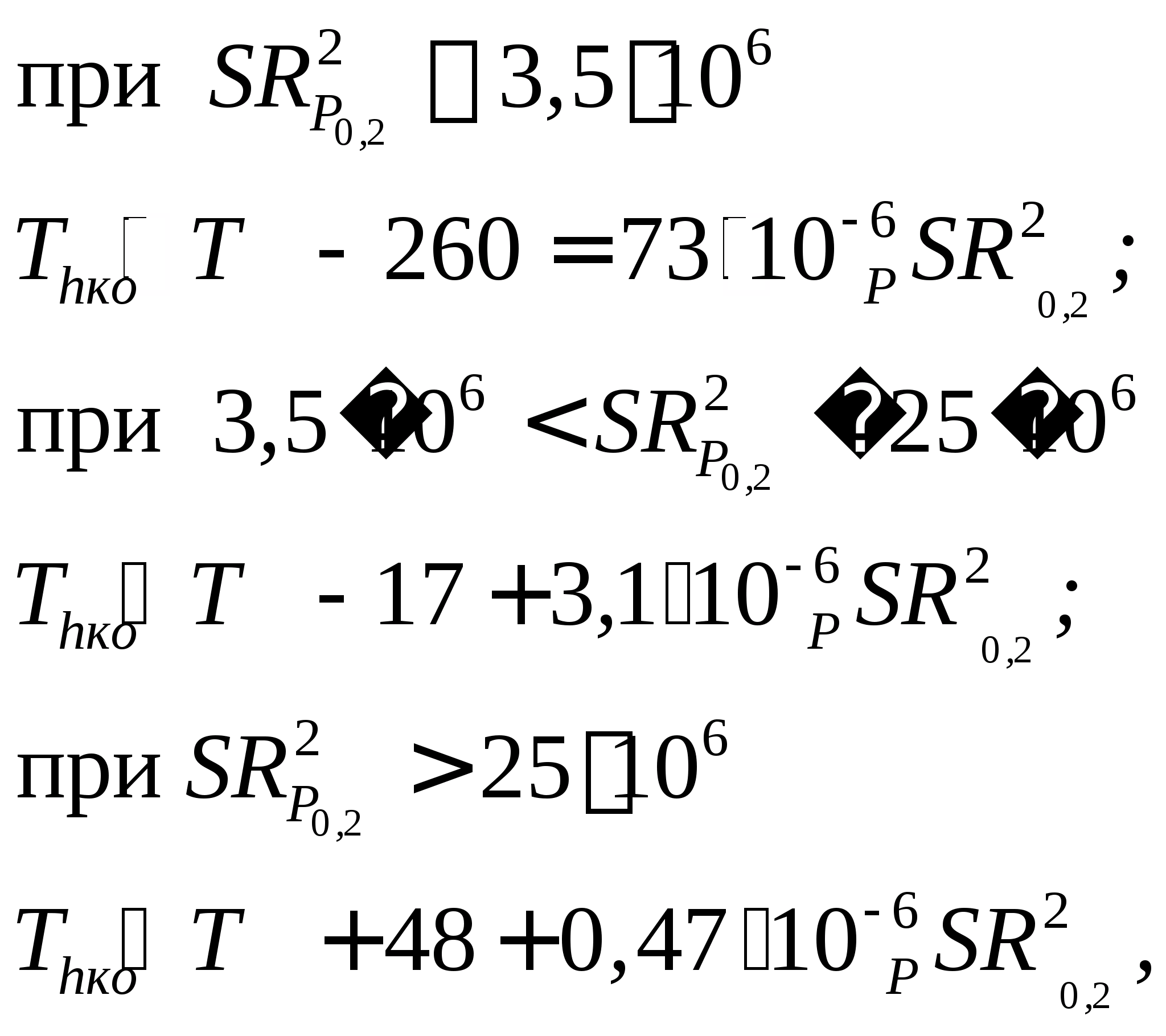
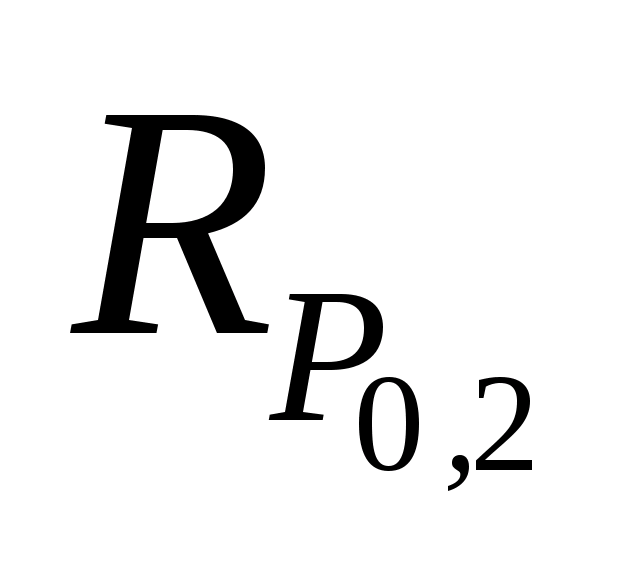
5.4. Requisitos para las pruebas hidráulicas (neumáticas)
5.4.1. Tiempo de mantenimiento de equipos y tuberías bajo presión R h durante las pruebas hidráulicas debe ser de al menos 10 min. Después de mantener, la presión de las pruebas hidráulicas disminuye a valores de 0,8 R h y la inspección de equipos y tuberías se realiza en lugares accesibles durante el tiempo necesario para la inspección. La temperatura mínima permitida del metal durante el mantenimiento debe determinarse de acuerdo con los estándares de cálculo de resistencia. La medición de la presión durante las pruebas hidráulicas debe realizarse utilizando dos manómetros o canales de medición verificados independientes. El error en la medición de la presión durante las pruebas hidráulicas, teniendo en cuenta la clase de precisión del sensor (manómetro), no debe exceder el ± 5 % del valor nominal de la presión de prueba. La clase de precisión del sensor (manómetro) debe ser de al menos 1,5. 5.4.2. Tiempo de espera bajo presión PAG h cuando se prueba después de la fabricación de accesorios con un diámetro interior de las tuberías de conexión de no más de 100 mm, se permite instalar de acuerdo con documentación técnica sobre el producto 5.4.3. Durante las pruebas hidráulicas, se permiten fluctuaciones de presión debido a cambios en la temperatura del fluido. Los valores permisibles de fluctuaciones de temperatura y presión en cada caso particular deben establecerse por cálculo o experimentalmente, mientras que la presión no debe exceder los límites inferior y superior según las cláusulas 5.2.1, 5.2.3. No se permite bajar la temperatura por debajo de la establecida según la cláusula 5.3. Se permite compensar las fugas previstas por el diseño de los sellos del eje de la bomba bombeando el medio de prueba. 5.4.4. Las pruebas hidráulicas se deben realizar con un medio no inflamable que no afecte negativamente al equipo ni a la tubería. Se establecen los requisitos para la calidad del entorno de prueba. especificaciones por producto y debe indicarse en los pasaportes de equipos y tuberías o en los certificados de fabricación de piezas y unidades de montaje de tuberías. 5.4.5. El control de la temperatura del metal debe realizarse mediante dispositivos de control térmico. No se podrá realizar el control de temperatura si la temperatura del líquido y la temperatura ambiente son superiores a la temperatura de las pruebas hidráulicas establecidas en la cláusula 5.3 La temperatura deberá ser controlada por sensores e instrumentos con un error total no superior al ± 3% de el valor máximo de la temperatura medida. 5.4.6. Al realizar pruebas hidráulicas de equipos y tuberías, se deben tomar medidas para evitar la acumulación de burbujas de gas en las cavidades llenas de líquido.5.5. Pruebas neumáticas
5.5.1. Presión de prueba neumática R R debe ser determinada al menos por la fórmula:(línea de fondo),
Donde Para R= 1,15 para equipos y tuberías; Para R= 1 para carcasas protectoras y carcasas de seguridad (carcasas). El límite superior es el mismo que en la Sección 5.2.1. Para elementos cargados con presión externa, la condición
Los requisitos de la cláusula 5.2.2 no son válidos para pruebas neumáticas. 5.5.2. Si hay una columna de metal líquido en el equipo y las tuberías durante la operación, que es imposible de tener durante las pruebas neumáticas, entonces el límite inferior de la presión de las pruebas neumáticas debe determinarse mediante la fórmula
Donde H- altura de la columna de metal líquido; - gravedad específica del metal líquido a la temperatura de diseño; R - presión de operación del gas por encima del nivel del metal líquido. 5.5.3. Durante las pruebas neumáticas de carcasas protectoras, carcasas de seguridad (carcasas), el equipo o las tuberías cubiertos por ellos pueden estar bajo presión externa, como resultado de lo cual puede ser necesario crear una contrapresión en el equipo o las tuberías. PAG gramo . En este caso, se debe hacer siguiente condición:
5.5.4. Al determinar el mínimo temperatura permitida metal debe guiarse por las instrucciones de la cláusula 5.3. 5.5.5. Durante las pruebas neumáticas, se deben observar los requisitos de las cláusulas 5.2.3, 5.2.4, 5.3, 5.4.1 (en términos de requisitos de error y mediciones y la clase de precisión del instrumento), cláusulas 5.4.3, 5.4.5 . 5.5.6. Tiempo de mantenimiento de equipos y tuberías bajo presión R R durante las pruebas neumáticas debe ser de al menos 30 min. Después de la exposición, se reduce la presión y se inspeccionan los equipos y las tuberías en lugares accesibles durante el tiempo requerido. La inspección se realiza a una presión determinada por el responsable de realizar los ensayos en base a condiciones de seguridad, pero en todos los casos esta presión no debe exceder de 0,85 R R . El tiempo de permanencia bajo presión para accesorios con un diámetro interior de tubería de conexión de no más de 100 mm durante las pruebas neumáticas está establecido por las condiciones técnicas de entrega. 5.5.7. Las válvulas de la tubería de llenado destinadas a las pruebas neumáticas y los instrumentos para medir la presión y la temperatura deben retirarse fuera de la sala en la que se encuentra el equipo probado, a un lugar seguro para el personal. Durante el aumento de la presión del gas en los equipos y tuberías probados, manteniendo bajo presión R R y reduciendo la presión al valor establecido para la inspección, el personal debe estar en lugar seguro.
5.6. Programas de pruebas hidráulicas (neumáticas)
5.6.1. Antes de realizar pruebas hidráulicas (neumáticas) de equipos y unidades de ensamblaje (partes) de tuberías, el fabricante debe elaborar un programa de producción (o instrucción tecnológica, proceso tecnológico) pruebas. 5.6.2. Para llevar a cabo pruebas hidráulicas (neumáticas) después de la instalación y durante la operación, la organización de diseño debe elaborar un programa de prueba completo, sobre la base del cual la administración de la central nuclear (o organización especializada determinado por la decisión del ministerio pertinente) se debe elaborar un programa de prueba de trabajo. (Edición modificada. Rev. No. 1). 5.6.3. El programa de producción (instrucción tecnológica, proceso tecnológico) de pruebas hidráulicas (neumáticas) de equipos y unidades de ensamblaje (partes) de tuberías después de la fabricación debe incluir los siguientes datos: 1) nombre del equipo o unidades de ensamblaje (partes) de tuberías; 2) presión de diseño; 3) presión de pruebas hidráulicas (neumáticas); 4) temperatura de las pruebas hidráulicas (neumáticas); 5) medios de prueba y requisitos para su calidad; 6) tasas permisibles de aumento y disminución de la presión; 7) índices permisibles de aumento y disminución de la temperatura; 8) tiempo de mantenimiento a la presión de prueba PAG h (PAG pag); 9) la presión a la que se realizará la inspección; 10) fuente de presión; 11) método de calentamiento del medio de prueba (si es necesario); 12) puntos de instalación de sensores (dispositivos) para control de presión y su clase de precisión; 13) puntos de instalación de sensores (dispositivos) para control de temperatura y su clase de precisión; 14) límites permisibles de fluctuaciones de presión y temperatura durante el mantenimiento; 15) requisitos de seguridad; 16) lugares de instalación de enchufes tecnológicos; 17) una lista de medidas organizativas, incluida la designación de personas responsables de las pruebas. El programa debe ser aprobado por el ingeniero jefe (director) del fabricante y acordado con la organización de diseño pertinente. 5.6.4. Un programa integral de pruebas hidráulicas (neumáticas) de sistemas, sus partes o ciertos tipos los equipos y tuberías después de la instalación y durante la operación deben incluir los siguientes datos: 1) el nombre y los límites del sistema bajo prueba (partes del sistema, equipos, tuberías); 2) presión de trabajo; 3) presión de pruebas hidráulicas (neumáticas); 4) temperatura de las pruebas hidráulicas (neumáticas); 5) medios de prueba y requisitos para su calidad; 6) tasas permisibles de aumento y disminución de la presión; 7) índices permisibles de aumento y disminución de la temperatura; 8) la presión a la que se realizará la inspección; 9) métodos para llenar y drenar el ambiente de prueba; 10) fuente de presión; 11) método de calentamiento del medio de prueba (si es necesario); 12) puntos de instalación de sensores (dispositivos) para control de presión; 13) puntos de instalación de sensores (dispositivos) para control de temperatura; 14) límites permisibles de fluctuaciones de presión y temperatura durante el mantenimiento. El programa integrado debe ser acordado por la dirección de la organización de diseño y aprobado por la administración de la central nuclear. (Edición modificada. Rev. No. 1). 5.6.5. programa de trabajo Las pruebas hidráulicas (neumáticas), además de la información enumerada en la cláusula 5.6.4, deben contener los siguientes datos: 1) especificación de los valores de presión y temperatura de las pruebas hidráulicas (neumáticas) de acuerdo con los pasaportes de los componentes del equipos y tuberías probados; 2) el lugar de conexión de la fuente de presión; 3) una lista de sensores e instrumentos utilizados para monitorear la presión y la temperatura, indicando la clase de precisión; 4) programa de prueba (etapas de aumento y disminución de la presión, aumento y disminución de la temperatura, tiempo de retención, etc.); 5) métodos para monitorear la condición de los equipos y tuberías probados durante la inspección y después de la finalización de las pruebas; 6) medidas de preparación para la prueba (indicando las válvulas a cerrar y abrir, limitando el sistema probado o parte de él); 7) una lista de lugares para quitar el aislamiento térmico; 8) medidas de protección contra el exceso de presión por encima de la de prueba; 9) requisitos de seguridad; diez) arreglos organizacionales(incluido el nombramiento de una persona responsable de las pruebas); 11) el número del programa integrado en base al cual se ha elaborado el programa de trabajo. El programa de trabajo debe ser aprobado por la administración de la central nuclear. (Edición modificada. Rev. No. 1). 5.6.6. Después de la finalización de las pruebas, se debe redactar un protocolo que incluya los siguientes datos: 1) el nombre de la empresa que realizó las pruebas; 2) el nombre del sistema probado (partes del sistema, equipo, tuberías, unidades de ensamblaje, partes); 3) presión de diseño (de trabajo); 4) temperaturas de diseño; 5) prueba de presión; 6) temperatura de prueba; 7) entorno de prueba; 8) tiempo de exposición a la presión de prueba; 9) la presión a la que se realiza la inspección; 10) número del programa de trabajo (producción); 11) resultado de la prueba; 12) firma del responsable y fecha.5.7. Evaluación de los resultados de las pruebas hidráulicas (neumáticas)
Se considera que los equipos y tuberías han pasado las pruebas hidráulicas (neumáticas), si no se encontraron fugas y roturas de metal durante las pruebas e inspección, durante la exposición de acuerdo con la cláusula 3.4.1, la caída de presión no superó los límites especificados. en la cláusula 5.4.3, y después de la prueba, no se revelaron deformaciones residuales visibles. Durante las pruebas hidráulicas (neumáticas) de equipos y unidades de ensamblaje (partes) de tuberías, las fugas a través de los sellos tecnológicos destinados a la prueba no son una señal de rechazo.Página 12 de 16
PRUEBAS NEUMÁTICAS
8.10. Se deben realizar pruebas neumáticas para tuberías de acero con una presión de trabajo que no supere los 1,6 MPa (16 kgf / cm 2) y temperaturas de hasta 250 ° C, montadas a partir de tuberías y piezas probadas en cuanto a resistencia y estanqueidad (densidad) por los fabricantes de acuerdo con GOST 3845-75 (al mismo tiempo, la presión de prueba de fábrica para tuberías, accesorios, equipos y otros productos y partes de la tubería debe ser un 20 % superior a la presión de prueba adoptada para la tubería instalada).
No se permite la instalación de accesorios de hierro fundido (excepto válvulas de hierro dúctil) durante la prueba.
8.11. El llenado de la tubería con aire y el aumento de la presión deben realizarse sin problemas a una velocidad de no más de 0,3 MPa (3 kgf / cm 2) por 1 hora. Inspección visual de la ruta (entrada a la zona de seguridad [peligrosa], pero sin descender a la zanja] está permitido a un valor de presión igual a 0,3 de prueba, pero no superior a 0,3 MPa (3 kgf/cm 2).
Durante el período de inspección de la ruta, se debe detener el aumento de presión.
Cuando se alcanza la presión de prueba, la tubería debe sujetarse para igualar la temperatura del aire a lo largo de la tubería. Después de igualar la temperatura del aire, la presión de prueba se mantiene durante 30 minutos y luego disminuye gradualmente a 0,3 MPa (3 kgf / cm 2), pero no superior a la presión de trabajo del refrigerante; a esta presión, las tuberías se inspeccionan con una marca de lugares defectuosos.
Las fugas se identifican por el sonido del aire que se escapa, por las burbujas al cubrir las juntas soldadas y otros lugares con emulsión jabonosa y por otros métodos.
Los defectos se eliminan solo cuando el exceso de presión se reduce a cero y el compresor se apaga.
8.12. Los resultados de las pruebas neumáticas preliminares se consideran satisfactorios si durante su realización no hubo caída de presión en el manómetro, no se encontraron defectos en soldaduras, bridas, tuberías, equipos y otros elementos y productos de la tubería, no hay signos de cortante o deformación de la tubería de tubería y soportes fijos.
8.13. Tuberías de redes de agua en sistemas cerrados Las tuberías de suministro de calor y condensado deben, por regla general, someterse a un lavado hidroneumático.
Se permite el lavado hidráulico con reutilizar enjuagar el agua pasándola a través de sumideros temporales instalados en la dirección del movimiento del agua en los extremos de las tuberías de suministro y retorno.
El lavado debe hacerse normalmente agua de proceso. Se permite el enjuague con agua corriente y potable con justificación en el proyecto para la realización de las obras.
8.14. Tuberías de redes de agua sistemas abiertos Las redes de suministro de calefacción y agua caliente deben lavarse hidroneumáticamente con agua potable hasta que el agua de lavado esté completamente clarificada. Después del lavado, las tuberías deben desinfectarse llenándolas con agua que contenga cloro activo a una dosis de 75-100 mg / l con un tiempo de contacto de al menos 6 horas Se permiten tuberías con un diámetro de hasta 200 mm y una longitud de hasta 1 km, de acuerdo con los organismos locales de los servicios sanitarios y servicio epidemiológico, no sometido a cloración y limitado a enjuague con agua, correspondiente a los requisitos de GOST 2874-82.
Después del lavado, los resultados del análisis de laboratorio de las muestras agua de lavado debe cumplir con los requisitos de GOST 2874-82. Se elabora una conclusión sobre los resultados del lavado (desinfección) por parte del servicio sanitario y epidemiológico.
8.15. La presión en la tubería durante el lavado no debe ser superior a la de trabajo. La presión de aire durante el lavado hidroneumático no debe exceder la presión de trabajo del refrigerante y no debe ser superior a 0,6 MPa (6 kgf / cm 2).
Las velocidades del agua durante el lavado hidráulico no deben ser inferiores a las velocidades de diseño del refrigerante indicadas en los planos de trabajo, y durante el lavado hidroneumático, exceder las calculadas en al menos 0,5 m/s.
8.16. Las tuberías de vapor deben purgarse con vapor y descargarse a la atmósfera a través de tuberías de purga especialmente instaladas con válvulas de cierre. Para calentar la tubería de vapor, todos los drenajes de arranque deben estar abiertos antes de la purga. La tasa de calentamiento debe garantizar la ausencia de choques hidráulicos en la tubería.
Las velocidades de vapor durante el soplado de cada sección deben ser al menos las velocidades de operación para los parámetros de diseño del refrigerante.
Contenido |
---|
Prueba neumática Las tuberías se llevan a cabo para verificar su resistencia y densidad o solo para la densidad. En este último caso, la tubería debe someterse a una prueba previa de resistencia. hidráulicamente. Amoníaco y tuberías de freón no se prueban para la resistencia hidráulica.
Se supone que las pruebas neumáticas se realizan con aire o un gas inerte, para lo cual utilizan compresores móviles o red de fábrica aire comprimido. Presión de prueba la resistencia y la longitud de la sección probada de la tubería del tendido sobre el suelo no deben exceder los valores especificados en la Tabla. 20
En casos excepcionales que surjan de los requisitos del proyecto, se permite realizar una prueba de resistencia neumática de tuberías con una desviación de los datos proporcionados en la tabla. En este caso, la prueba debe llevarse a cabo en estricta conformidad con una instrucción especialmente desarrollada (para cada caso) que garantice una correcta seguridad en el trabajo.
Se prohíben las pruebas de resistencia neumática de hierro fundido elevado, así como de tuberías de vidrio y faolíticas. En el caso de la instalación de accesorios de hierro fundido en tuberías de acero (excepto accesorios hechos de hierro dúctil), se permite la prueba de resistencia neumática a una presión que no exceda los 4 kgf/cm2, al mismo tiempo, todos los accesorios de hierro fundido deben someterse a una prueba preliminar prueba hidráulica fuerza de acuerdo con GOST 356-59.
La presión en la tubería bajo prueba debe elevarse gradualmente, inspeccionándola cuando alcance: 0,6 de la presión de prueba - para tuberías con presión de trabajo de hasta 2 kgf/cm2; 0,3 y 0,6 de la presión de prueba - para tuberías con una presión de trabajo superior a 2 kgf/cm2. Al inspeccionar la tubería, no se permite un aumento de presión. La inspección final se lleva a cabo a la presión de operación y se combina con una prueba de estanqueidad de la tubería. Al mismo tiempo, la estanqueidad de las juntas soldadas, las juntas de brida y los prensaestopas se verifica cubriéndolas con jabón u otra solución. Golpeando con oro en un oleoducto ubicado bajo presión, No permitido. Los resultados de la prueba neumática se consideran satisfactorios si durante la prueba de resistencia no hubo caída de presión en el manómetro y durante la prueba de estanqueidad posterior no se encontraron fugas o huecos en las soldaduras, juntas de brida y prensaestopas.
Oleoductos que transportan potentes sustancias toxicas y otros productos con propiedades tóxicas, los gases licuados del petróleo, los gases inflamables y activos, así como los líquidos inflamables y combustibles transportados a temperaturas superiores a su punto de ebullición, se someten a una prueba adicional de densidad. En este caso, la prueba se lleva a cabo con la determinación de la caída de presión. Las tuberías de taller que transportan los productos enumerados anteriormente se someten a pruebas de densidad adicionales junto con el equipo al que están conectadas.
La prueba de densidad con la determinación de la caída de presión solo se puede realizar después de que las temperaturas dentro de la tubería se hayan igualado, para lo cual se deben instalar termómetros al principio y al final de la sección de prueba. Duración del exámen tuberías entre tiendas en la densidad con la determinación de la caída de presión se establece por el proyecto; debe ser por lo menos 12 H. La caída de presión en la tubería durante su prueba de densidad está determinada por la fórmula:
donde ∆ R- valor de caída de presión, %;
R estafa y p inicio es la suma de las presiones manométrica y barométrica al final y al comienzo de la prueba, respectivamente, kgf/cm2;
T estafa y T comienzo -absoluto temperatura del aire o gas, respectivamente, al final y al comienzo de la prueba grado
La presión y temperatura del aire o gas en la tubería se determina como el promedio aritmético de las lecturas de todos los manómetros y termómetros instalados en la tubería.
donde D BH- diámetro interior de la tubería probada, milímetro Si la tubería consta de secciones de diferentes diámetros, su diámetro interno promedio se determina mediante la fórmula:
Tubería entre talleres con paso condicional 250 milímetro aprobar prueba adicional sobre el. densidad si la caída de presión en él es 1 h como porcentaje de la presión de prueba no es más de: 0,1 - cuando se transportan productos tóxicos; 0.2 - al transportar gases explosivos, inflamables, combustibles y activos (incluidos los licuados). Al probar tuberías de otros diámetros, las tasas de caída en ellas se determinan multiplicando las cifras anteriores por un factor de corrección calculado por la fórmula:
L 1 , L 2 , ... L n- longitudes de las secciones correspondientes de la tubería, milímetro;
donde re 1 , re 2 , ... re n- diámetros internos de las secciones de tubería, metro.
Durante la duración de las pruebas neumáticas, tanto en interiores como en exteriores, es necesario establecer un área protegida y señalizarla con banderas. Distancia mínima en cualquier dirección desde la tubería bajo prueba hasta el límite de la zona: en tendido aéreo - 25 metro, y con metro - 10 metro. Se instalan puestos de control para monitorear el área protegida. Durante el aumento de presión en la tubería y al probar su resistencia, no se permite que las personas permanezcan en el área protegida, excepto las personas especialmente designadas para este fin e instruidas.
Se redacta un acta para los resultados de las pruebas neumáticas de la tubería.
1. ¿En qué orden se realizan las pruebas de resistencia neumática?
2. ¿Cómo se realiza una prueba neumática de estanqueidad de tuberías?
3. ¿Cómo se realiza una prueba de resistencia neumática de tuberías con determinación de caída de presión?