5. HIDRAULIČKA (PNEUMATSKA) ISPITIVANJA
5.1. Opći zahtjevi
5.1.1. Hidraulička (pneumatska) ispitivanja provode se radi provjere čvrstoće i gustoće opreme, cjevovoda, njihovih dijelova i montažnih jedinica, opterećenih tlakom. 5.1.2. Hidraulička ispitivanja provode se: 1) nakon što je proizvođač proizveo opremu ili elemente cjevovoda koji su isporučeni za ugradnju; 2) nakon ugradnje opreme i cjevovoda; 3) u tijekom rada oprema i cjevovodi opterećeni pritiskom vode, pare ili mješavine pare i vode. 5.1.3. Umjesto hidrauličkih ispitivanja, dopušteno je provoditi pneumatska ispitivanja opreme i cjevovoda opterećenih plinskim tlakom, koji rade pod vakuumom, u kontaktu s tekućim metalnim rashladnim sredstvom, kao i sigurnosnih kućišta (okućišta) nuklearnih elektrana s reaktorima na brzim neutronima i zaštitnim školjke ACT. Mogućnost takve zamjene mora odobriti Gosatomnadzor Rusije. Dopušteno je ne provoditi hidraulička ispitivanja (nakon proizvodnje i tijekom rada) eksperimentalnih i istraživačkih trupa nuklearnih reaktora rade pod pritiskom težine tekućine koja ih ispunjava, s tim da se tijekom proizvodnog procesa vrši 100% kontrola zavarenih spojeva ultrazvučnom detekcijom grešaka ili radiografskom metodom i površinskim metodama detekcije grešaka. 5.1.4. Hidraulička (pneumatska) ispitivanja nakon ugradnje i tijekom rada provode se u rokovima navedenim u točki 8.2.6. 5.1.5. Provođenje hidrauličkih (pneumatskih) ispitivanja nakon ugradnje tijekom puštanja u pogon opreme i cjevovoda, kao i tijekom rada (osim slučajeva popravka posebno navedenih u ovom dokumentu) je obvezno. 5.1.6. Hidrauličko ispitivanje dijelova ili montažnih jedinica cjevovoda proizvedenih na mjestima ugradnje može se kombinirati s hidrauličkim ispitivanjem nakon dovršetka montaže. 5.1.7. Oprema i cjevovodi nakon proizvodnje i ugradnje moraju biti podvrgnuti hidrauličkim ispitivanjima prije nanošenja zaštitnih antikorozivni premazi odnosno toplinske izolacije. Na opremi i cjevovodima koji su tijekom rada u kontaktu s tekućim metalnim rashladnim sredstvom, dopušteno je postaviti toplinsku izolaciju prije hidrauličkih ispitivanja s navedenom rashladnom tekućinom. Dopušteno je izvršiti metalizaciju (bez nanošenja premazi) zavareni spojevi cjevovoda prije hidrauličkog ispitivanja, ako se to ne može učiniti nakon dovršetka instalacije, što treba navesti u projektnu dokumentaciju . 5.1.8. Hidrauličko (pneumatsko) ispitivanje opreme i cjevovoda tijekom rada treba provesti nakon uklanjanja toplinske izolacije na mjestima navedenim u točki 2.1.9, kao i navedenim u projektnoj dokumentaciji. 5.1.9. Hidraulička ispitivanja pojedinih dijelova i montažnih jedinica opreme i cjevovoda nakon njihove izrade ne smiju se provoditi u sljedećim slučajevima: 1) proizvođač provodi hidraulička ispitivanja tih dijelova i montažnih jedinica u sklopu proširenih montažnih jedinica ili proizvoda; 2) proizvođač opreme koja ne sadrži zavarene spojeve I i I i kategoriju B opreme od perlitnih čelika ili visokokromiranih čelika vrši kontinuiranu ultrazvučnu i radiografsku kontrolu osnovnog metala i zavarenih spojeva, austenitnih čelika i legure željeza i nikla - kontinuirana radiografska kontrola osnovnog metala i zavarenih spojeva, uz sve ostale zahtjeve PC-a i projektne dokumentacije; 3) proizvođač opreme skupine C od perlitnih čelika i visokokromiranih čelika provodi kontinuirano ultrazvučno ispitivanje svih zavarenih spojeva, kao i njihovo radiografsko ispitivanje u dvostrukom volumenu u odnosu na propisani PC, te austenitnih čelika i željeza -nikl čelici - kontinuirano radiografsko ispitivanje svih zavarenih spojeva; u tom slučaju moraju se poštovati svi ostali zahtjevi računala i projektne dokumentacije; 4) proizvođač dijelova i montažnih jedinica cjevovoda skupine B i C izrađenih od čelika klase perlita i visokokromiranih čelika provodi kontinuirano ultrazvučno ispitivanje svih zavarenih spojeva, kao i radiografsko ispitivanje zavarenih spojeva II a, II za kategorije u količini od 100%, II c, II nv i III a kategorije - u količini od 50%, III c - u količini od 25%, a od čelika austenitnog razreda - kontinuirana radiografska kontrola svih zavarenih spojeva, dok se moraju poštivati svi ostali zahtjevi računala i projektne dokumentacije; osim toga, dodatni kapilarni ili magnetski pregled obrađenih površina (provrta, prijelaza, zavoja cijevi, itd.) i ultrazvučni ili radiografski pregled metala u područjima koncentracije naprezanja i na područjima podvrgnutim deformaciji većoj od 5% tijekom proizvodnje (savijanja i produženi krajevi cijevi, izduženi vratovi i sl.) i u mjeri utvrđenoj projektnom dokumentacijom (za cjevovode skupine C ova se dodatna kontrola ne smije provoditi). 5.1.10. Standarde za ocjenu kvalitete za kontrolu prema točki 5.1.9 treba usvojiti za osnovni metal prema standardima ili specifikacijama za relevantne materijale i poluproizvode, a za zavarene spojeve - prema PC-u. 5.1.11. Hidraulička (pneumatska) ispitivanja pojedinih dijelova (npr. cijevi) kod proizvođača ne smiju se provoditi ako su prošli hidraulička ispitivanja kod dobavljača tih proizvoda i nakon toga nisu bili podvrgnuti radnjama tijekom kojih je materijal tih proizvoda dijelovi su podvrgnuti plastičnoj deformaciji. 5.1.12. Hidraulička (pneumatska) ispitivanja nakon proizvodnje elemenata opreme i cjevovoda opterećenih tijekom rada vanjskim tlakom mogu se provoditi pod opterećenjem unutarnji pritisak.5.2. Određivanje tlaka hidrauličkih (pneumatskih) ispitivanja
5.2.1. Hidraulički ispitni tlak mora se odrediti barem prema formuli:(Poanta)
I ne više od tlaka pri kojem je ukupna membranska naprezanja jednaka 1,35 [ ] Th, a zbroj općih ili lokalnih membranskih i općih naprezanja na savijanje će doseći 1,7 [ ] Th(Gornja granica). U gornjoj formuli Do = 1.25 za opremu i cjevovode i Do= 1 za zaštitne školjke i sigurnosna kućišta (kućišta), R - projektni tlak pri ispitivanju u pogonu proizvođača ili radni tlak tijekom ispitivanja nakon instalacije i tijekom rada, [ ] Th- nazivno dopušteno naprezanje pri temperaturi hidrauličkog ispitivanja T h za strukturni element, [ ] T - nazivni dopušteni napon pri projektnoj temperaturi T smatra strukturnim elementom. Za elemente opterećene vanjskim pritiskom također mora biti zadovoljen sljedeći uvjet:
R h 1,25 [R].
Bilješka. vrijednosti [ ] Th , [ ] T, opća i lokalna membrana i opća naprezanja savijanja; [ R] - dopušteni vanjski tlak pri temperaturi hidrauličkog ispitivanja određuje se prema Standardima za proračun čvrstoće. 5.2.2. Pod pritiskom R do 0,49 MPa (5 kgf / cm 2) vrijednosti R h trebao bi biti veći od 1,5 R, ali ne manje od 0,2 MPa (2 kgf / cm 2). Pod pritiskom R više od 0,49 MPa (5 kgf / cm 2) vrijednosti P h mora se odrediti iz uvjeta iz točke 5.2.1, ali ne manje od ( R + 0,29) MPa (( R+ 3) kgf / cm 2). Ovi zahtjevi se ne odnose na opremu i cjevovode s tekućim metalnim rashladnim sredstvom. 5.2.3. U slučaju da se hidraulička (pneumatska) ispitivanja provode na sustavu ili krugu koji se sastoji od opreme i cjevovoda koji rade na različitim radnim pritiscima i (ili) projektnim temperaturama, ili su izrađeni od materijala s različitim [ ] Th i/ili [ ] T, tada tlak hidrauličkih (pneumatskih) ispitivanja ovog sustava (kruga) treba uzeti jednakim minimalna vrijednost gornja granica ispitnih tlakova, odabrana od svih relevantnih vrijednosti za opremu i cjevovode koji čine sustav (petlja). 5.2.4. Vrijednosti hidrauličkog ispitnog tlaka za opremu i montažne jedinice (blokove) cjevovoda proizvođač mora navesti u putovnici opreme i potvrdi o proizvodnji dijelova i montažnih jedinica cjevovoda. Vrijednosti tlaka hidrauličkih (pneumatskih) ispitivanja sustava (krugova) mora odrediti projektantska organizacija i prijaviti ih vlasniku opreme i cjevovoda, koji te vrijednosti određuje na temelju podataka sadržanih u putovnicama opreme i cjevovoda koji dovršavaju sustav (krug).
5.3. Određivanje temperature hidrauličkih (pneumatskih) ispitivanja
5.3.1. Hidraulička (pneumatska) ispitivanja opreme i cjevovoda moraju se provoditi na temperaturi ispitnog medija pri kojoj temperatura metala ispitivane opreme i cjevovoda neće biti niža od minimalno dopuštene temperature, određene u skladu s Proračunom čvrstoće. Standardi. U ovom slučaju, u svim slučajevima, temperatura testa i okoliš ne smije biti ispod 5 °C. 5.3.2. Dopušteno je provesti hidraulička (pneumatska) ispitivanja nakon proizvodnje ili ugradnje bez provođenja proračuna prema točki 5.3.1 pri temperaturi metala od najmanje 5 °C u sljedećim slučajevima: 1) proizvod je izrađen od korozije otporni austenitni čelik, obojena ili legura željeza i nikla; 2) proizvod je izrađen od materijala s granom tečenja pri temperaturi od 20 ° C manjom od 295 MPa (30 kgf / mm 2) i ima najveću debljinu stijenke ne veću od 25 mm; 3) proizvod je izrađen od materijala s granom tečenja pri temperaturi od 20 ° C manjom od 590 MPa (60 kgf / mm 2) i. ima najveću debljinu stijenke ne veću od 16 mm. Također je dopušteno, bez provođenja izračuna prema točki 5.3.1, odrediti minimalnu dopuštenu temperaturu metala tijekom hidrauličkih ispitivanja T h iz sljedećih omjera: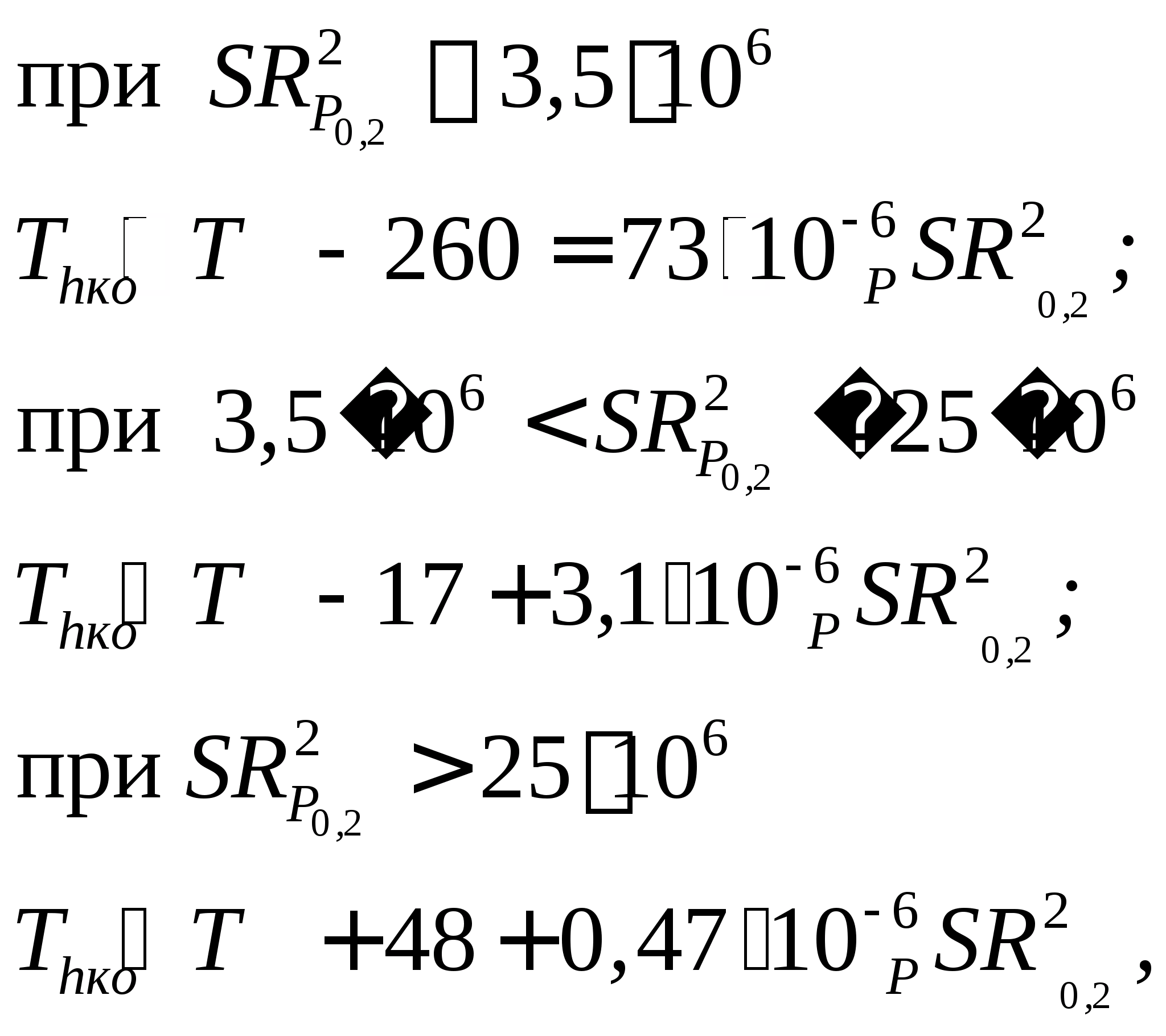
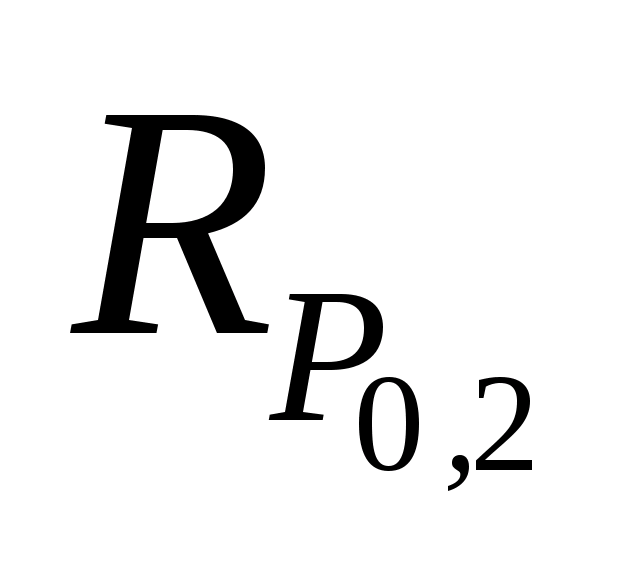
5.4. Zahtjevi za hidrauličko (pneumatsko) ispitivanje
5.4.1. Vrijeme držanja opreme i cjevovoda pod pritiskom R h tijekom hidrauličkih ispitivanja treba biti najmanje 10 min. Nakon držanja, tlak hidrauličkih ispitivanja smanjuje se na vrijednosti od 0,8 R h a pregled opreme i cjevovoda obavlja se na pristupačnim mjestima za vrijeme potrebno za pregled. Najmanju dopuštenu temperaturu metala tijekom držanja treba odrediti prema standardima izračuna čvrstoće. Mjerenje tlaka tijekom hidrauličkih ispitivanja treba provesti pomoću dva neovisna provjerena manometra ili mjernih kanala. Pogreška u mjerenju tlaka tijekom hidrauličkih ispitivanja, uzimajući u obzir klasu točnosti senzora (manometar), ne smije biti veća od ± 5% nazivne vrijednosti ispitnog tlaka. Klasa točnosti senzora (manometar) mora biti najmanje 1,5. 5.4.2. Vrijeme držanja pod pritiskom P h pri ispitivanju nakon proizvodnje armatura s unutarnjim promjerom spojnih cijevi ne većim od 100 mm, dopuštena je ugradnja prema tehnička dokumentacija na proizvodu. 5.4.3. Tijekom hidrauličkog ispitivanja dopuštene su fluktuacije tlaka zbog promjena temperature tekućine. Dopuštene vrijednosti kolebanja temperature i tlaka u svakom pojedinom slučaju treba utvrditi proračunski ili eksperimentalno, dok tlak ne smije prelaziti donju i gornju granicu prema točkama 5.2.1, 5.2.3. Nije dopušteno snižavanje temperature ispod postavljene prema točki 5.3. Dopušteno je nadoknaditi propuštanje predviđeno dizajnom brtvi vratila crpke pumpanjem ispitnog medija. 5.4.4. Hidraulička ispitivanja moraju se provesti korištenjem nezapaljivog medija koji ne utječe negativno na opremu ili cjevovod. Utvrđeni su zahtjevi za kvalitetu ispitnog okruženja tehnički podaci po proizvodu i moraju biti naznačeni u putovnicama opreme i cjevovoda ili u potvrdama o proizvodnji dijelova i montažnih jedinica cjevovoda. 5.4.5. Kontrolu temperature metala treba provoditi termoregulacijskim uređajima. Kontrola temperature ne smije se provoditi ako su temperatura tekućine i temperatura okoline viša od temperature hidrauličkih ispitivanja utvrđenih u točki 5.3. Temperatura se mora kontrolirati senzorima i instrumentima s ukupnom pogreškom koja ne prelazi ± 3% od maksimalna vrijednost izmjerene temperature. 5.4.6. Prilikom provođenja hidrauličkih ispitivanja opreme i cjevovoda moraju se poduzeti mjere za sprječavanje nakupljanja mjehurića plina u šupljinama ispunjenim tekućinom.5.5. Pneumatska ispitivanja
5.5.1. Pneumatski ispitni tlak R R mora biti barem određena formulom:(Poanta),
Gdje Do R= 1,15 za opremu i cjevovode; Do R= 1 za zaštitne školjke i sigurnosna kućišta (kućišta). Gornja granica je ista kao u odjeljku 5.2.1. Za elemente opterećene vanjskim pritiskom, uvjet
Zahtjevi iz točke 5.2.2 ne vrijede za pneumatska ispitivanja. 5.5.2. Ako u opremi i cjevovodima tijekom rada postoji stup tekućeg metala, koji je nemoguće imati tijekom pneumatskih ispitivanja, tada se donja granica tlaka pneumatskih ispitivanja treba odrediti po formuli
Gdje H- visina stupca tekućeg metala; - specifična težina tekućeg metala na projektnoj temperaturi; R - radni tlak plina iznad razine tekućeg metala. 5.5.3. Tijekom pneumatskog ispitivanja zaštitnih omotača, sigurnosnih kućišta (kućišta), opreme ili cjevovoda koji su njima pokriveni mogu biti pod vanjskim tlakom, zbog čega može biti potrebno stvoriti protutlak u opremi ili cjevovodima P g . U ovom slučaju, to se mora učiniti sljedeći uvjet:
5.5.4. Pri određivanju minimuma dopuštena temperatura metala treba voditi prema uputama iz točke 5.3. 5.5.5. Tijekom pneumatskih ispitivanja, moraju se poštovati zahtjevi klauzula 5.2.3, 5.2.4, 5.3, 5.4.1 (u pogledu zahtjeva za pogrešku i mjerenja te klase točnosti instrumenta), klauzula 5.4.3, 5.4.5 . 5.5.6. Vrijeme držanja opreme i cjevovoda pod pritiskom R R tijekom pneumatskih ispitivanja treba biti najmanje 30 min. Nakon izlaganja tlak se smanjuje, a oprema i cjevovodi se pregledavaju na pristupačnim mjestima u potrebnom vremenu. Provjera se provodi pod tlakom koji određuje osoba odgovorna za provođenje ispitivanja na temelju sigurnosnih uvjeta, ali u svim slučajevima taj tlak ne smije biti veći od 0,85 R R . Vrijeme držanja pod tlakom za spojeve s unutarnjim promjerom spojnih cijevi ne većim od 100 mm tijekom pneumatskih ispitivanja određeno je tehničkim uvjetima za isporuku. 5.5.7. Ventili cjevovoda za punjenje namijenjeni za pneumatsko ispitivanje i instrumenti za mjerenje tlaka i temperature moraju se ukloniti izvan prostorije u kojoj se ispitna oprema nalazi, na mjesto sigurno za osoblje. Tijekom porasta tlaka plina u ispitivanoj opremi i cjevovodima, držanje pod tlakom R R i smanjenje tlaka na vrijednost postavljenu za inspekciju, osoblje mora biti u sigurno mjesto.
5.6. Programi hidrauličkog (pneumatskog) ispitivanja
5.6.1. Prije provođenja hidrauličkog (pneumatskog) ispitivanja opreme i montažnih jedinica (dijelova) cjevovoda, proizvođač mora izraditi proizvodni program (ili tehnološku uputu, tehnološki proces) testovi. 5.6.2. Za provođenje hidrauličkih (pneumatskih) ispitivanja nakon ugradnje i tijekom rada, projektna organizacija mora izraditi sveobuhvatan program ispitivanja, na temelju kojeg uprava NEK (odn. specijalizirana organizacija utvrđeno rješenjem nadležnog ministarstva) potrebno je izraditi program radnog ispitivanja. (Promijenjeno izdanje. Rev. br. 1). 5.6.3. Proizvodni program (tehnološka uputa, tehnološki proces) hidrauličkog (pneumatskog) ispitivanja opreme i montažnih jedinica (dijelova) cjevovoda nakon proizvodnje mora sadržavati sljedeće podatke: 1) naziv opreme ili montažnih jedinica (dijelova) cjevovoda; 2) projektni tlak; 3) tlak hidrauličkih (pneumatskih) ispitivanja; 4) temperatura hidrauličkih (pneumatskih) ispitivanja; 5) ispitne medije i zahtjeve za njihovu kvalitetu; 6) dopuštene stope povećanja i smanjenja tlaka; 7) dopuštene brzine porasta i smanjenja temperature; 8) vrijeme držanja na ispitnom tlaku P h (P str); 9) tlak pod kojim se vrši pregled; 10) izvor pritiska; 11) način zagrijavanja ispitnog medija (ako je potrebno); 12) mjesta ugradnje senzora (uređaja) za kontrolu tlaka i njihova klasa točnosti; 13) mjesta ugradnje senzora (uređaja) za kontrolu temperature i njihova klasa točnosti; 14) dopuštene granice kolebanja tlaka i temperature tijekom držanja; 15) sigurnosni zahtjevi; 16) mjesta ugradnje tehnoloških utikača; 17) popis organizacijskih mjera, uključujući imenovanje odgovornih osoba za ispitivanje. Program mora odobriti glavni inženjer (direktor) proizvođača i usuglasiti ga s odgovarajućom projektantskom organizacijom. 5.6.4. Opsežan program hidrauličkog (pneumatskog) ispitivanja sustava, njihovih dijelova odn određene vrste oprema i cjevovodi nakon ugradnje i tijekom rada trebaju sadržavati sljedeće podatke: 1) naziv i granice sustava koji se ispituje (dijelovi sustava, oprema, cjevovodi); 2) radni tlak; 3) tlak hidrauličkih (pneumatskih) ispitivanja; 4) temperatura hidrauličkih (pneumatskih) ispitivanja; 5) ispitne medije i zahtjeve za njihovu kvalitetu; 6) dopuštene stope povećanja i smanjenja tlaka; 7) dopuštene brzine porasta i smanjenja temperature; 8) tlak pod kojim se vrši pregled; 9) metode punjenja i dreniranja ispitnog okoliša; 10) izvor pritiska; 11) način zagrijavanja ispitnog medija (ako je potrebno); 12) mjesta ugradnje senzora (uređaja) za kontrolu tlaka; 13) mjesta ugradnje senzora (uređaja) za kontrolu temperature; 14) dopuštene granice kolebanja tlaka i temperature tijekom držanja. Integrirani program mora dogovoriti uprava projektantske organizacije i odobriti ga uprava NEK. (Promijenjeno izdanje. Rev. br. 1). 5.6.5. Radni program hidraulička (pneumatska) ispitivanja, osim podataka navedenih u točki 5.6.4., moraju sadržavati sljedeće podatke: 1) specifikaciju vrijednosti tlaka i temperature hidrauličkih (pneumatskih) ispitivanja prema putovnicama komponenti uređaja ispitana oprema i cjevovodi; 2) mjesto priključka izvora tlaka; 3) popis korištenih senzora i instrumenata za praćenje tlaka i temperature s naznakom razreda točnosti; 4) raspored ispitivanja (faze porasta i pada tlaka, porast i pad temperature, vrijeme držanja itd.); 5) metode praćenja stanja opreme i cjevovoda koji se ispituju tijekom pregleda i nakon završetka ispitivanja; 6) mjere za pripremu za ispitivanje (označavanje ventila koji se zatvaraju i otvaraju, ograničavanje ispitivanog sustava ili njegovog dijela); 7) popis mjesta za skidanje toplinske izolacije; 8) mjere zaštite od prekomjernog tlaka iznad ispitnog; 9) sigurnosni zahtjevi; deset) organizacijski aranžmani(uključujući imenovanje osobe odgovorne za testiranje); 11) broj integriranog programa na temelju kojeg je izrađen program rada. Program rada mora odobriti uprava NEK. (Promijenjeno izdanje. Rev. br. 1). 5.6.6. Nakon obavljenih ispitivanja mora se sastaviti protokol koji sadrži sljedeće podatke: 1) naziv poduzeća koje je provelo ispitivanja; 2) naziv ispitivanog sustava (dio sustava, oprema, cjevovodi, montažne jedinice, dijelovi); 3) projektni (radni) tlak; 4) projektne temperature; 5) ispitivanje tlakom; 6) ispitna temperatura; 7) testno okruženje; 8) vrijeme izlaganja ispitnom tlaku; 9) tlak pri kojem se vrši pregled; 10) broj radnog (proizvodnog) programa; 11) rezultat ispitivanja; 12) potpis odgovorne osobe i datum.5.7. Vrednovanje rezultata hidrauličkih (pneumatskih) ispitivanja
Smatra se da su oprema i cjevovodi prošli hidraulička (pneumatska) ispitivanja, ako tijekom ispitivanja i pregleda nisu pronađena curenja i lomovi metala, tijekom izlaganja prema točki 3.4.1, pad tlaka nije prelazio navedene granice u točki 5.4.3, a nakon ispitivanja nisu otkrivene vidljive preostale deformacije. Prilikom hidrauličkog (pneumatskog) ispitivanja opreme i montažnih jedinica (dijelova) cjevovoda, propuštanje kroz tehnološke brtve namijenjene ispitivanju nije znak odbijanja.Stranica 12 od 16
PNEUMATSKA ISPITIVANJA
8.10. Pneumatska ispitivanja trebaju se provoditi za čelične cjevovode s radnim tlakom koji ne prelazi 1,6 MPa (16 kgf / cm 2) i temperaturama do 250 ° C, montirane od cijevi i dijelova koje su proizvođači ispitali na čvrstoću i nepropusnost (gustoću) u skladu s GOST-om 3845-75 (istodobno, tvornički ispitni tlak za cijevi, armature, opremu i druge proizvode i dijelove cjevovoda mora biti 20% veći od ispitnog tlaka usvojenog za ugrađeni cjevovod).
Ugradnja armatura od lijevanog željeza (osim ventila od nodularnog željeza) nije dopuštena za vrijeme trajanja ispitivanja.
8.11. Punjenje cjevovoda zrakom i podizanje tlaka treba obavljati glatko, brzinom ne većom od 0,3 MPa (3 kgf / cm 2) na 1 sat Vizualni pregled trase (ulaza u sigurnosnu [opasnu) zonu, ali bez spuštanje u rov] dopušteno je pri vrijednosti tlaka, jednakoj 0,3 testa, ali ne više od 0,3 MPa (3 kgf / cm 2).
Za vrijeme pregleda trase, povećanje tlaka mora biti zaustavljeno.
Kada se postigne ispitni tlak, cjevovod se mora držati kako bi se izjednačila temperatura zraka duž duljine cjevovoda. Nakon izjednačavanja temperature zraka, ispitni tlak se održava 30 minuta, a zatim se postupno smanjuje na 0,3 MPa (3 kgf / cm 2), ali ne više od radnog tlaka rashladne tekućine; pri tom tlaku, cjevovodi se pregledavaju s oznakom neispravnih mjesta.
Curenja se prepoznaju po zvuku zraka koji curi, po mjehurićima pri prekrivanju zavarenih spojeva i drugih mjesta sapunastom emulzijom i drugim metodama.
Nedostaci se otklanjaju tek kada se višak tlaka smanji na nulu i kompresor se isključi.
8.12. Rezultati preliminarnih pneumatskih ispitivanja smatraju se zadovoljavajućim ako tijekom njihovog provođenja nije došlo do pada tlaka na mjeraču tlaka, nisu pronađeni nedostaci na zavarenim spojevima, prirubničkim spojevima, cijevima, opremi i drugim elementima i proizvodima cjevovoda, nema znakova smicanje ili deformacija cjevovoda cjevovoda i fiksnih nosača.
8.13. Cjevovodi vodovodnih mreža u zatvoreni sustavi Cjevovodi za opskrbu toplinom i kondenzat u pravilu trebaju biti podvrgnuti hidropneumatskom pranju.
Hidrauličko ispiranje je dopušteno sa ponovno koristiti ispiranje vode propuštanjem kroz privremene jame postavljene u smjeru kretanja vode na krajevima dovodnog i povratnog cjevovoda.
Pranje bi se normalno trebalo obaviti industrijska voda. Ispiranje komunalnom i pitkom vodom dopušteno je uz obrazloženje u projektu za izradu radova.
8.14. Cjevovodi vodovodnih mreža otvoreni sustavi mreže za grijanje i toplu vodu moraju se hidropneumatski ispirati pitkom vodom do potpunog bistrenja vode za ispiranje. Nakon ispiranja, cjevovodi se moraju dezinficirati punjenjem vodom koja sadrži aktivni klor u dozi od 75-100 mg/l s vremenom kontakta od najmanje 6 sati Dozvoljeni su cjevovodi promjera do 200 mm i duljine do 1 km, u dogovoru s lokalnim tijelima sanitarne i epidemiološke službe, ne smiju biti podvrgnute kloriranju i ograničene na ispiranje vodom, u skladu sa zahtjevima GOST 2874-82.
Nakon pranja, rezultati laboratorijske analize uzoraka voda za pranje mora biti u skladu sa zahtjevima GOST 2874-82. O rezultatima pranja (dezinfekcije) sanitarno-epidemiološke službe donosi se zaključak.
8.15. Tlak u cjevovodu tijekom ispiranja ne smije biti veći od radnog. Tlak zraka tijekom hidropneumatskog ispiranja ne smije prelaziti radni tlak rashladne tekućine i ne smije biti veći od 0,6 MPa (6 kgf / cm 2).
Brzine vode tijekom hidrauličkog ispiranja ne smiju biti niže od projektnih brzina rashladne tekućine navedene na radnim crtežima, a tijekom hidropneumatskog ispiranja premašiti proračunske za najmanje 0,5 m/s.
8.16. Parovodi se moraju pročišćavati parom i ispuštati u atmosferu kroz posebno postavljene cijevi za pročišćavanje sa zapornim ventilima. Za zagrijavanje parnog cjevovoda svi odvodi za pokretanje moraju biti otvoreni prije pročišćavanja. Brzina zagrijavanja treba osigurati odsutnost hidrauličnih udara u cjevovodu.
Brzine pare tijekom puhanja svake sekcije moraju biti najmanje radne brzine za projektne parametre rashladne tekućine.
Sadržaj |
---|
Pneumatski test provode se cjevovodi kako bi se provjerila njihova čvrstoća i gustoća ili samo gustoća. U potonjem slučaju, cjevovod mora biti prethodno ispitan na čvrstoću. hidraulički. Amonijak i freonski cjevovodi nisu ispitani na hidrauličku čvrstoću.
Pneumatska ispitivanja bi se trebala provoditi zrakom ili inertnim plinom za koji se koriste mobilni kompresori ili tvorničke mreže potisnut zrak. Ispitni tlakčvrstoća i duljina ispitivanog dijela cjevovoda nadzemnog polaganja ne smiju prelaziti vrijednosti navedene u tablici. 20.
U iznimnim slučajevima, koji proizlaze iz zahtjeva projekta, dopušteno je provesti ispitivanje pneumatske čvrstoće cjevovoda s odstupanjem od podataka navedenih u tablici. U tom slučaju, ispitivanje se mora provesti u strogom skladu s posebno razvijenim (za svaki slučaj) uputama koje osiguravaju odgovarajuću sigurnost na radu.
Zabranjeno je ispitivanje pneumatske čvrstoće povišenog lijevanog željeza, kao i faolitskih i staklenih cjevovoda. U slučaju ugradnje armatura od lijevanog željeza na čelične cjevovode (osim spojnica od nodularnog željeza), dopušteno je ispitivanje pneumatske čvrstoće pri tlaku koji ne prelazi 4 kgf / cm 2, u isto vrijeme, svi okovi od lijevanog željeza moraju proći preliminarnu analizu hidraulički testčvrstoća u skladu s GOST 356-59.
Tlak u ispitivanom cjevovodu treba postupno podizati, provjeravajući ga kada dostigne: 0,6 ispitnog tlaka - za cjevovode s radnim tlakom do 2 kgf / cm 2; 0,3 i 0,6 ispitnog tlaka - za cjevovode s radnim tlakom iznad 2 kgf / cm 2. Prilikom pregleda cjevovoda nije dopušteno povećanje tlaka. Završni pregled provodi se pod radnim tlakom i kombinira se s ispitivanjem nepropusnosti cjevovoda. Istodobno se provjerava nepropusnost zavarenih spojeva, prirubničkih spojeva i žlijezda premazivanjem sapunom ili drugom otopinom. Tapkanje zlatom na cjevovodu koji se nalazi pod pritiskom, nije dozvoljeno. Rezultati pneumatskog ispitivanja smatraju se zadovoljavajućim ako tijekom ispitivanja čvrstoće nije došlo do pada tlaka na mjeraču tlaka, a tijekom naknadnog ispitivanja nepropusnosti nisu pronađena propuštanja ili praznine u zavarenim spojevima, prirubničkim spojevima i žljebovima.
Potentni transportni cjevovodi otrovne tvari i drugi proizvodi toksičnih svojstava, ukapljeni naftni plinovi, zapaljivi i aktivni plinovi, kao i zapaljive i zapaljive tekućine koje se transportiraju na temperaturama iznad vrelišta, podvrgavaju se dodatnom ispitivanju gustoće. U tom slučaju, ispitivanje se provodi s određivanjem pada tlaka. Trgovinski cjevovodi koji transportiraju gore navedene proizvode prolaze dodatna ispitivanja gustoće zajedno s opremom na koju su spojeni.
Ispitivanje gustoće s određivanjem pada tlaka može se provesti tek nakon izjednačavanja temperatura unutar cjevovoda, za što se termometri moraju postaviti na početku i na kraju ispitnog dijela. Trajanje testa međuradnički cjevovodi na gustoću s određivanjem pada tlaka postavlja se projektom; mora biti najmanje 12 h. Pad tlaka u cjevovodu tijekom ispitivanja gustoće određuje se formulom:
gdje je ∆ R- vrijednost pada tlaka, %;
R kon i P početak je zbroj manometarskog i barometarskog tlaka na kraju i početku ispitivanja, respektivno, kgf / cm 2;
T con i T početak -apsolutni temperatura zraka odnosno plin, na kraju i početku ispitivanja st.
Tlak i temperatura zraka ili plina u cjevovodu određuju se kao aritmetički prosjek očitanja svih mjerača tlaka i termometara ugrađenih na cjevovod.
gdje D BH- unutarnji promjer ispitivanog cjevovoda, mm. Ako se cjevovod sastoji od dijelova različitih promjera, njegov prosječni unutarnji promjer određuje se formulom:
Međuradnički cjevovod s uvjetnim prolazom 250 mm proći dodatni test na gustoće ako je pad tlaka u njemu 1 h kao postotak ispitnog tlaka nije veći od: 0,1 - pri prijevozu otrovnih proizvoda; 0,2 - pri prijevozu eksplozivnih, zapaljivih, zapaljivih i aktivnih plinova (uključujući ukapljene). Prilikom ispitivanja cjevovoda drugih promjera, stope pada u njima određuju se množenjem gornjih brojki s korekcijskim faktorom izračunatim po formuli:
L 1 , L 2 , ... L n- duljine odgovarajućih dionica cjevovoda, mm;
gdje D 1 , D 2 , ... D n- unutarnji promjeri dijelova cjevovoda, m.
Za vrijeme trajanja pneumatskih ispitivanja, kako u zatvorenom tako i na otvorenom, potrebno je uspostaviti zaštićeni prostor i obilježiti ga zastavicama. Minimalna udaljenost u bilo kojem smjeru od ispitivanog cjevovoda do granice zone: at nadzemno polaganje - 25 m, a s podzemnom - 10 m. Za nadzor zaštićenog područja postavljena su kontrolna mjesta. Tijekom porasta tlaka u cjevovodu i pri ispitivanju čvrstoće u štićenom prostoru nije dopušten boravak osoba, osim za to posebno određenih i upućenih osoba.
O rezultatima pneumatskih ispitivanja cjevovoda sastavlja se akt.
1. Kojim redoslijedom se provode ispitivanja pneumatske čvrstoće?
2. Kako se provodi pneumatsko ispitivanje cjevovoda na nepropusnost?
3. Kako se provodi ispitivanje pneumatske čvrstoće cjevovoda uz određivanje pada tlaka?